Modifications > Mast |
|
|
New
masthead - the original masthead was built of cast aluminum and lacked a
spinnaker crane. Bristol had the masthead, the mast step and the spreader
sockets custom fabricated; but after some research I was lucky enough to
find Metalmast Marine, in
Putnam, CT. One of the owners was involved in the spar work for Bristol at
that time. They made a new masthead that bolted on perfectly. The original
masthead was open with no guard to keep the halyards from jumping their
sheaves, and allowing water inside the mast. The new masthead is sealed to
keep out any rain, and the sheaves are properly covered. The smaller
antenna is for a cell phone. |
I
have removed all the gear from the masthead in this photo. The aluminum is
weathered from 10 years of salt air, but because I used silicone sealant on
the thread of all the tapped screws, everything came off easily. |
Another
view of the Metalmast masthead showing the spinnaker crane. You can see
clearly when I used Teflon gaskets under the fittings; the aluminum is still
bright. |
This
photo shows how effective the Teflon gaskets and the silicone sealant are
at preventing galvanic corrosion between the aluminum and the stainless
steel fittings. The aluminum underneath is clean and bright. |
Here
is an example of the level of quality of Metalmast's work. Notice the welds
on the underside of the spinnaker crane. |
A
close up of the quality of the welds in this assembly. |
Here
is everything removed from the masthead. Other than polishing some of the
aluminum and stainless, it will all go back on, using the same screws. |
Here
is an example of the thin Teflon gasket I cut for the stainless brackets
that mounted on the masthead. The screw holes were made with a paper hole
punch. |
Finally
a shot of one of the aluminum halyard sheaves showing the pressed in bronze
bearing. The folks at Metalmast do very high quality work. I highly
recommend them. |
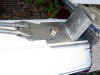 Originally,
the reason I started researching the spars at Bristol was because of a
chapter in
Jud Henderson's wonderful book on rigging. He notes the dangers of using
cast aluminum under pressure--the perfect example being spreader sockets,
which can literally explode without warning . And guess what: Bristol used
these cheesy, weathered, cast aluminum spreader sockets. Metalmast
made me new stainless steel sockets and tapered aluminum spreaders, It's your rig
folks. The new spreaders and sockets were around $300. Think about it. |
Here
you see the hounds added for the inner forestay. The hounds are a Schaefer
model that fit perfectly. It is attached with 1/4" machine screws tapped
into the mast. Note that all the fasteners are isolated from the aluminum
and potential corrosion with silicone sealant. I also laid thin sheets of
Teflon® between anything stainless and the painted spar
(any inert material, like Delrin®
for instance, would work). If not protected in
this way or with a similar type of isolation, the Awlgrip paint would have
bubbled and lifted from galvanic corrosion. |
In
order to counter the forward bending effect of the inner forestay I added
running backstay tangs at the height of the hounds. The tangs are Schaefer
parts, thru-bolted with a 3/8" s/s bolt. The back stays are vinyl covered
3/16" 7x9 wire that terminate at the level of the mast winches. I attach
4-part block and tackle to each for tensioning.
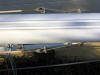 |
The
Hood Seafurl system is mounted to the bow using two similarly bent tangs,
thru-bolted through the tube of the drum, and mounted to the edge of the
Windline anchor roller. |
Here
is a close up of the tangs attached to the furling tube. |
To
mount the other end of the tangs to the anchor roller, I drilled a 5/16"
hole through the edge and secured a bolt. |
The
bolt protrudes about 3/4" to allow the tangs to be bolted in place. |
When
I rewired the mast I added pvc conduit to protect the wires. It's 1.25 thin
wall pipe--plenty of room for the wires. |
To
hold the conduit in place, I pop riveted it every 6 feet to the inside front
of the mast. |